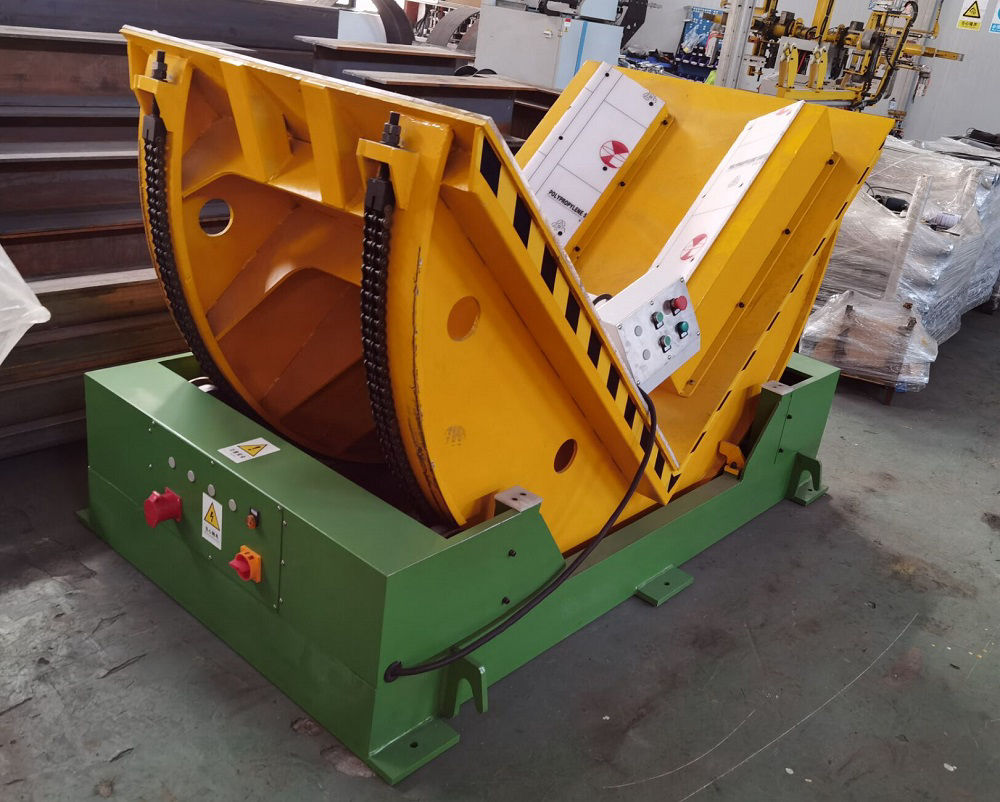
Introduction:
In the manufacturing industry, mold upender machines offer a powerful solution to increase productivity without compromising the quality of mold products.
These machines from FHOPE come equipped with unique features that optimize the manufacturing process, enabling manufacturers to enhance production efficiency while maintaining high-quality standards.
Key features such as self-lubricating copper sleeve bearings, electrical components with leakage protection, overload circuit breakers, and multiple fiber switches and mechanical protection devices contribute to operational safety and improved productivity.
Optimizing Process Flow and Equipment Utilization:
The introduction of mold upender machines allows manufacturers to optimize the overall process flow and enhance equipment utilization.
Our machines streamline the flipping process, reducing the need for manual labor and increasing production capacity.
By automating the flipping process, manufacturers can save time and resources, resulting in improved efficiency.
FHOPE’s mold upender takes special design of bearings.
The utilization of self-lubricating copper sleeve bearings is crucial for enhancing equipment reliability and minimizing downtime.
These bearings offer durability and high-temperature resistance, ensuring smooth and efficient operation without the need for frequent maintenance or lubrication.
As a result, production interruptions are minimized, leading to increased productivity.
Furthermore, mold upender machines incorporate advanced electrical components with leakage protection and overload circuit breakers.
These safety features prevent electrical hazards and equipment malfunctions, ensuring a secure working environment for operators.
By minimizing the risk of electrical issues, manufacturers can maintain a steady production flow and maximize output.
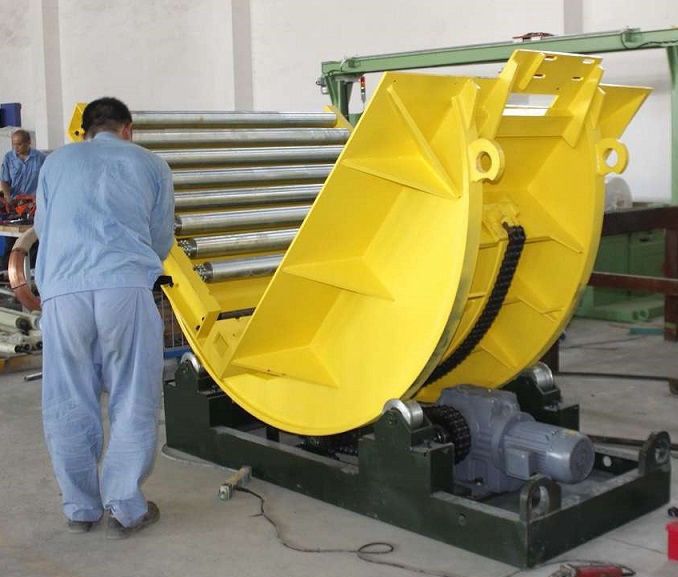
Enhancing Operational Safety:
Operational safety is paramount in any manufacturing environment.
Mold flip machines by FHOPE are designed with multiple fiber switches and mechanical protection devices to ensure the safety of operators and equipment.
Fiber switches act as limit switches, providing additional safety measures by preventing over-rotation or exceeding weight limits.
These switches allow the machine to operate within specified parameters, protecting both the molds and the machinery.
Mechanical protection devices, such as safety cages or barriers, create a physical barrier between operators and moving parts, reducing the risk of accidents during the flipping process.
These devices are engineered to withstand external forces and provide a secure working environment for operators, further enhancing operational safety.
Maintaining Quality Standards:
While increasing productivity is important, maintaining high-quality standards is equally crucial.
Mold flip machines offer precise control and stability during the flipping process, minimizing the risk of damage to the molds.
Additionally, the automated nature of these machines ensures consistency in the flipping action, resulting in uniform and high-quality mold products.
To ensure quality control, manufacturers should implement rigorous inspection and quality assurance protocols throughout the production process.
Regular checks and adherence to quality control standards help identify and address any potential issues, ensuring that the final mold products meet the required specifications.
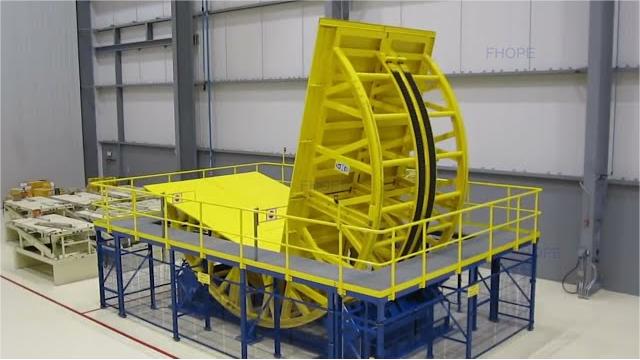
Conclusion:
Mold upender machines provide manufacturers with a powerful tool to increase productivity while upholding high-quality standards.
They can increase output without sacrificing quality.
By optimizing process flow, enhancing equipment utilization, and incorporating safety features such as self-lubricating copper sleeve bearings, electrical protection systems, and mechanical safety devices, these machines streamline operations and improve efficiency.
Manufacturers must also place a strong emphasis on maintaining operational safety and implementing rigorous quality control measures to ensure that the final mold products meet the required standards.
With the integration of mold flip machines, manufacturers can achieve significant productivity gains, enhance product quality, and remain competitive in the dynamic manufacturing industry.
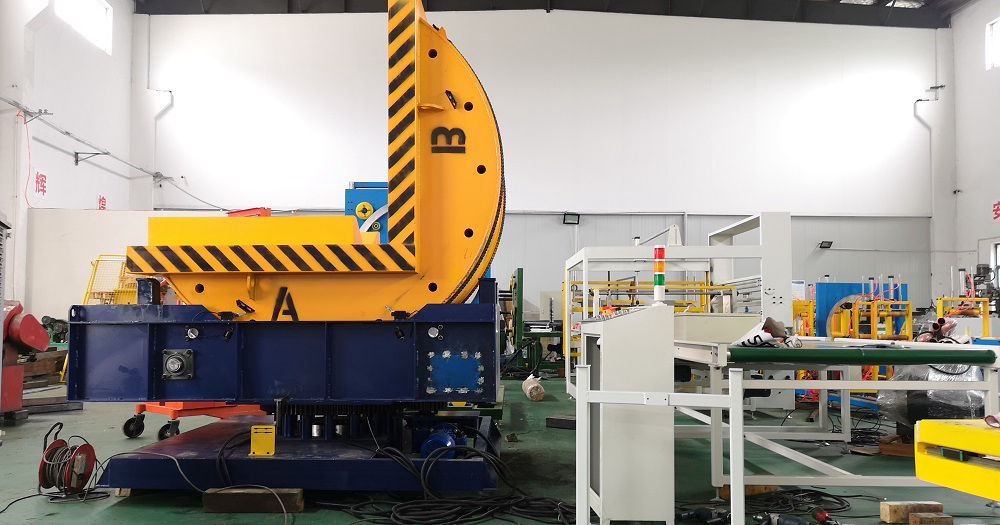